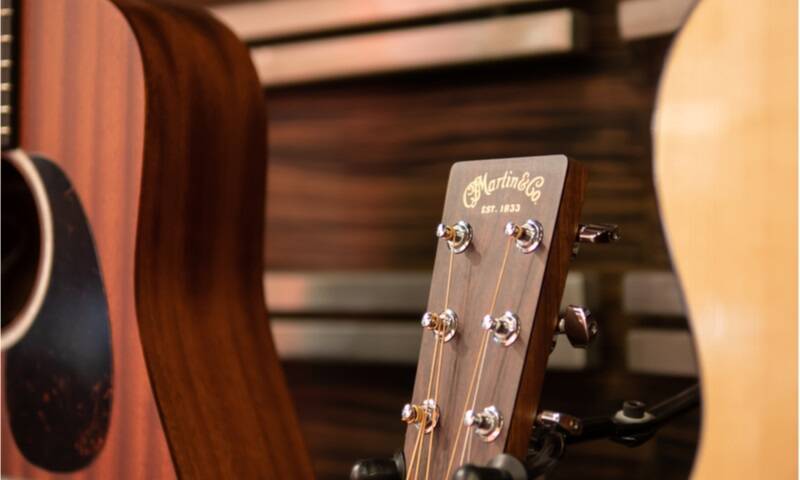
In the past century, the guitar-manufacturing business has become saturated with dozens of widely recognized brands and hundreds of lesser known ones. From Gibson to Fender to Ibanez and Takamine, there’s no shortage of selection for anyone seeking to buy a high quality instrument that will serve them for years to come.
Most guitarists have their guitar brand of choice, the one that they swear by and claim is better than any other guitar. If you want to buy a gift for a guitarist and money is no object, just ask them what their favorite guitar brand is. If you buy them one of these guitars, you’ll have their gratitude and respect in perpetuity!
While guitarists may debate which guitar manufacturer makes the best guitars, there’s one opinion shared by virtually all guitarists: Martin acoustic guitars are the best money can buy. With a tradition that goes back nearly two hundred years, Martin has perfected the art of building guitars that serve as the gold standard for this type of instrument.
The birth of a brand
In the 1830s, guitars were artisanally manufactured. Guitar shops would painstakingly craft guitars from wood, steel and glue over the course of several weeks, creating a unique but very expensive instrument in the process. In the 1830s, a new guitar cost more than a reliable riding horse, making them exclusive to the upper class.
It was in this industry that Christian F. Martin moved from his home in Germany to the lurid metropolis of New York City. With a substantial amount of experience under his belt from building guitars in Austria and Germany, Martin set to work building his own finely crafted, ornately decorated guitars.
Over the years, Martin made a long succession of innovations to the design of the flat-top acoustic guitar, incrementally making it into the instrument we see on stages and around campfires today. By the 1910s, C.F. Martin had grown to be a nationally recognized brand that provided the industry with the golden standard for this type of instrument.
The innovations made by the Martin guitar company were so extensive in fact that pre-war models are universally used to gauge the quality of newer guitars. From the headstock of the Fender Stratocaster to the 20 fret standard neck length, the influences of C.F. Martin and his marvelous guitars can be seen everywhere in the world of music.
How they’re made
Objectively speaking, Martin guitars haven’t changed all that much since their design was perfected back in the 1920s. With a silhouette that is as timeless as it is functional, the current day Martin guitar is made in much the same way that it was back before the first world war. So what does this look like in practice? Let’s find out!
The wood
Before a Martin guitar takes shape, it rests in the trunk of a tree in a well cared for and sustainably maintained forest. These hardwood trees are the backbone of a good guitar, so every tree that is felled is checked previously for blemishes, knots and imperfections that might impact the final product.
Martin guitars are made from a variety of different woods, varying from model to model according to the customer’s preferences and choices. Regardless of which type of wood is chosen, one thing remains consistent across all Martin guitars: the quality of the end result is immaculate and the sound is unparalleled!
Once the lumber is felled, the logs are loaded up onto trucks and sent to their destination: the Martin guitar factory in Nazareth, Pennsylvania. Here, they’ll be stripped, cut, planed and sanded, ready to be carved and moulded into brand new Martin signature guitars. Once it’s been prepared, this wood will move on to the next step in the production line.
The woodwork
Now that the wood for the guitars has arrived at the factory, each individual slab will be visually inspected by a Martin employee to ensure that there are no imperfections or blemishes that might lead to a sub-par product. Taking their time, the inspector will thoroughly mark any wood that is unfit for production, after which this wood will be disposed of responsibly.
After the best materials have been chosen, they’ll be moved to the woodshop. Here, the components that make up each guitar will be stamped, cut or carved into their appropriate shapes. Unlike many companies that prioritize quantity over quality, Martin woodworkers painstakingly double- and triple-check their work to make sure it’s up to snuff.
Several of the components used in Martin guitars require additional preparation; the sides, for example, must be soaked in a softening solution, pressed in a mould and then allowed to dry and harden before they can be used, a process that takes great care and precision. Nevertheless, thanks in large part to the unparalleled skill of the craftsmen and women at work here, the process is surprisingly efficient.
The workshop
Once all the components of the guitar are in the proper form, it’s time to put the guitar together. This is a job that is reserved for only the most experienced luthiers at Martin, as the process requires absolute precision as well as unimpeachable instinct and intuition. If a brace, fret or tuning knob is so much two or three millimeters out of place, the guitar would be less than perfect, and possibly even unplayable.
The process of assembling a Martin guitar is slow and methodical. Nothing can be rushed, nor can anything be overlooked. The braces must be fitted perfectly in order to bear the incredible tension exerted upon the body and neck, while the frets must be placed with micrometer-scale precision lest the guitar produce buzz or dead tones.
In spite of the exacting nature of this task, the luthiers at Martin are so skilled and experienced that they are able to build a finished guitar in as little as three weeks from start to finish. While more ornate or complex designs often take longer, the relative efficiency of this process simply cannot be understated.
Off to market
From start to finish, the journey of a Martin guitar living tree to fully finished guitar can take weeks, months or in rare cases, years. Nevertheless, once the guitar is finally finished, it’s time for it to meet its new owner. At this point, each guitar is set up by a luthier and carefully packaged in a custom case, ready to be shipped.
Lower end Martin guitars (if you can call such a finely crafted instrument by this crude term) will be sent off to guitar shops and guitarists across the country to be played by musicians and hobbyists from all walks of life. While these models may not have the ornate touches you’d find on a custom Martin, they’re still the same lovingly crafted instruments at their core.
While they often take longer to manufacture, high-end custom Martin guitars are seldom sent to music stores. These guitars are truly one of a kind, and are most often sold one at a time to the most passionate guitar aficionados and professional musicians for whom money is no object. Regardless how much you pay for your Martin, one thing is for sure: you won’t regret buying it!
Conclusion
Whether you’re thinking of purchasing a Martin to improve your experience as a guitarist or you’ve received your big break as a musician and want to celebrate by buying a good acoustic, trust us when we say that these guitars cannot be matched. They’re instruments of the highest quality, and there are very few who would disagree. We hope you enjoy yours!
Add comment
Comments